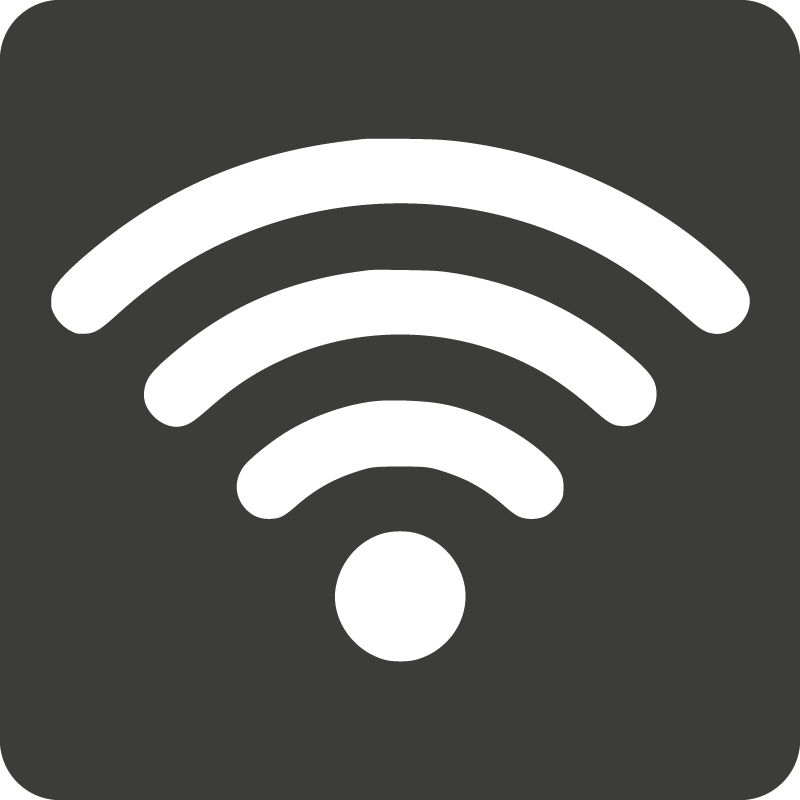
RANGE 5 km
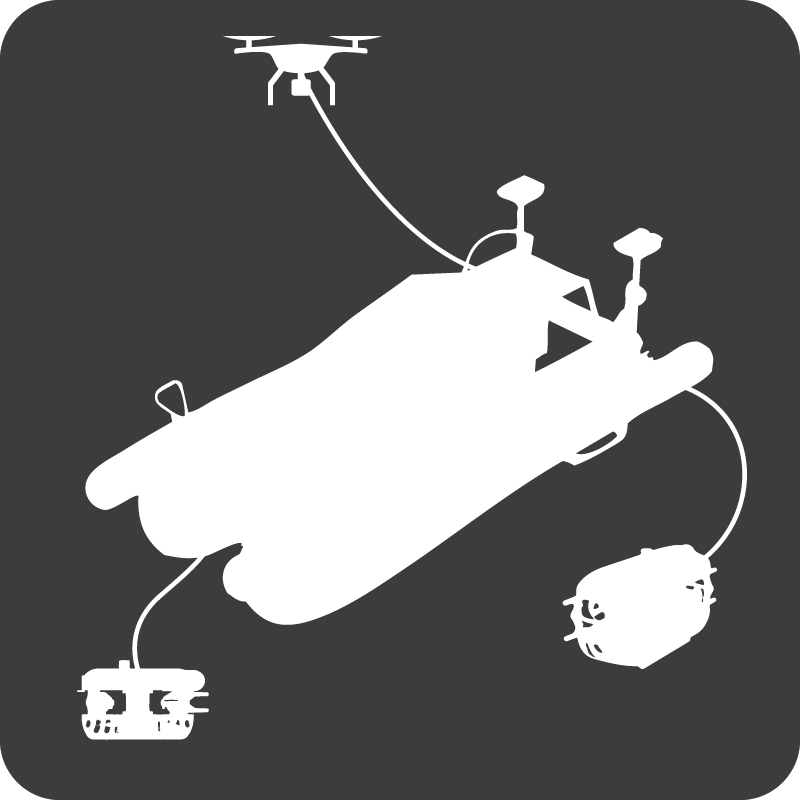
ROV and UAV launching
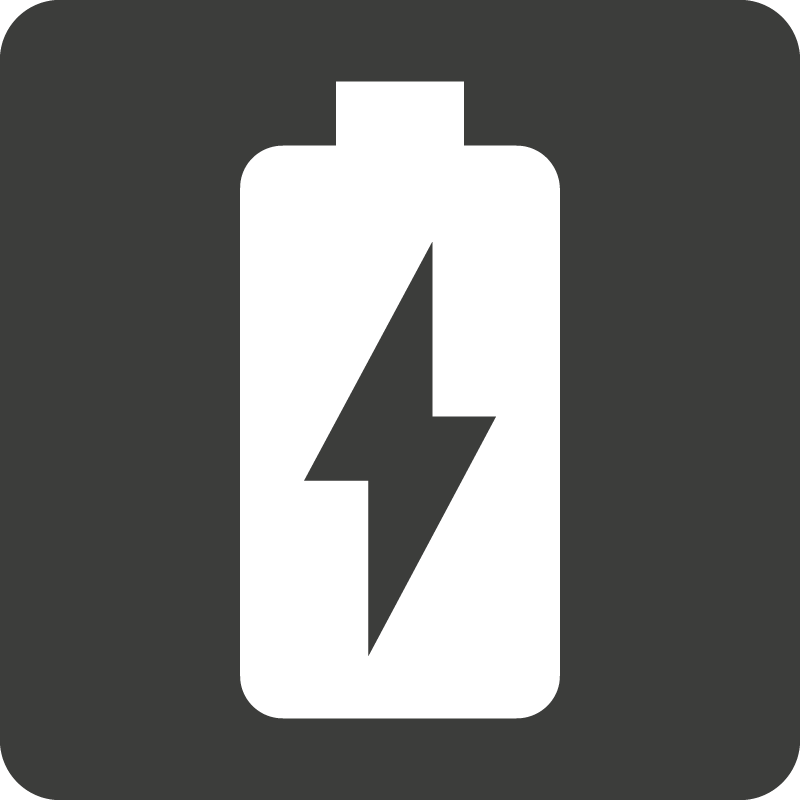
Up to 8 days autonomy

Payload 500 kg
Fits inside a 20′ container
Power and endurance
The SeaCAT USV is a sea going catamaran type drone designed for automatic or remotely controlled inspection and survey missions on offshore infrastructures. SeaCAT offers an innovative multi-drone plateform by supporting an ROV and a UAV to carry out inspection below and above water with a single control interface.
Its aluminium fabrication completed by inflatable lateral tubes makes it perfectly shockproof while lightweight and harmless for the inspected infrastructures. The overall system fits inside a 20’ container to ease transport and reduce mob/demob cost.
With no operator at sea, saving up to 85% operational cost and reducing up to 50 times CO2 emissions compared to conventional spreads, SeaCAT offers a safe, clean and affordable solution for offshore IMR campaigns.
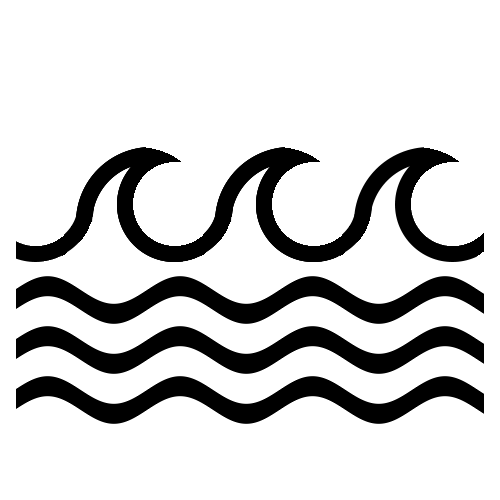
Harsh conditions
The SeaCAT system is specially designed for severe weather conditions (wind, waves, current, low visibility):
– UAV : over 50 knots wind
– USV : sea state 4-5 in operation, 6 in transit
– ROV : current up to 4.5 knots in all directions
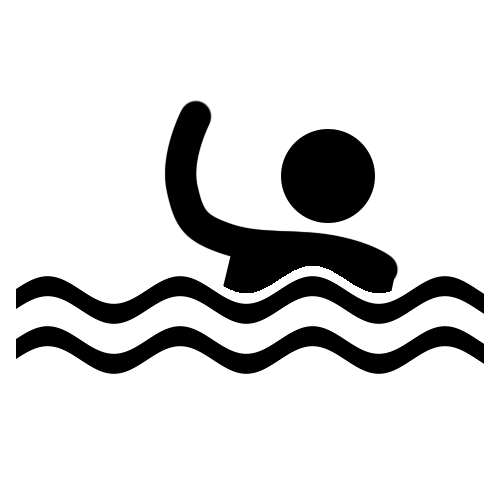
Human safety
No operators at sea !
System piloted through WiFi (+ radio/satellite during transit)
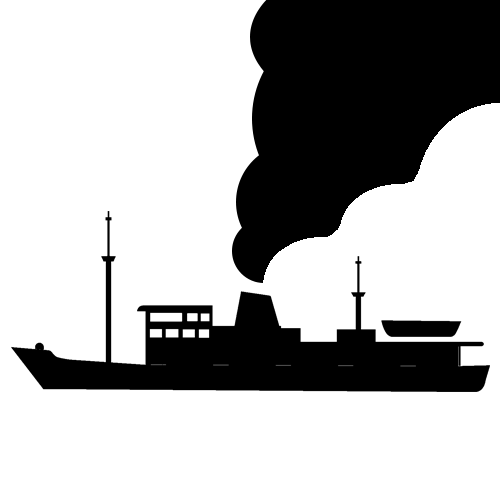
Environmental impact
The SeaCAT USV fuel consumption is under 100 liters per day, i.e. 20 to 50 times less than conventional DP survey/ROV vessels.
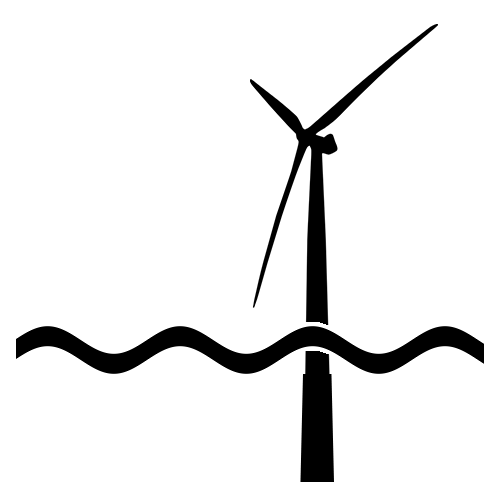
Inspection above/below water
The SeaCAT system is a multi-drone combination:
-1 UAV for the aerial parts
-1 USV for the seabed survey
-1 ROV for the submerged structures
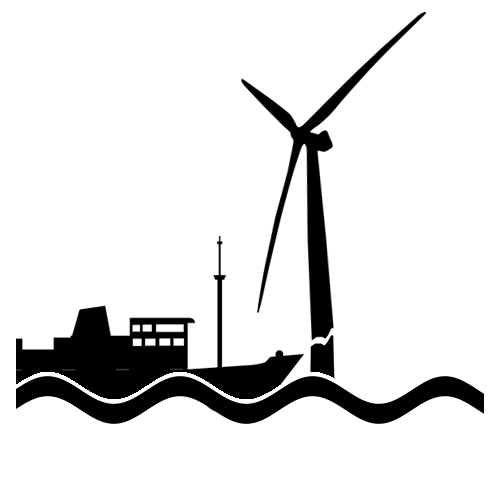
Risk for infrastructures
The SeaCAT USV is a light (1,075 Kg) and compact (6.83 m) vehicle presenting a very little threat for offshore structures. Besides, its peripheral rib tubes offer an efficient protection in case of accidental shock.
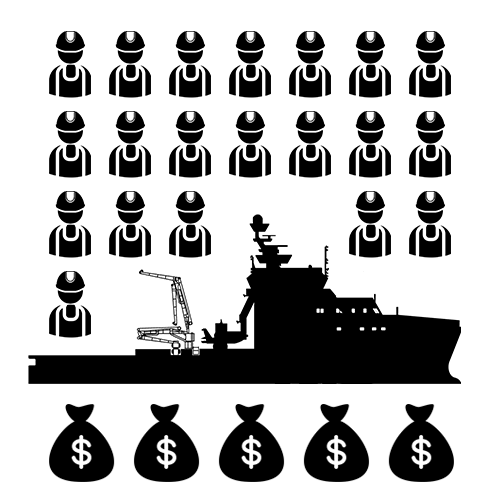
O&M costs
The SeaCAT requires only 6 onshore operators for 24/24 operations (3 x 8 hours shift), allowing a cost saving of 65 to 85% compared to conventional vessels.
Inquiry
Thank you for filling in the form to receive a quote or information. Fields marked with (*) are compulsory. Find a dealer